产品目录
液体涡轮流量计
液体流量计
水流量计
油流量计
气体涡轮流量计
椭圆齿轮流量计
电磁流量计
涡街流量计
蒸汽流量计
孔板流量计
旋进旋涡流量计
热式气体质量流量计
转子流量计
浮子流量计
靶式流量计
气体流量计
超声波流量计
磁翻板液位计
浮子液位计
浮球液位计
玻璃管液位计
雷达液位计
超声波液位计
投入式液位计
压力变送器
差压变送器
液位变送器
温度变送器
热电偶
热电阻
双金属温度计
推荐产品
联系我们
- 金湖凯铭仪表有限公司
- 联系电话:15195518515
- 在线客服:1464856260
- 电话:0517-86801009
- 传真号码:0517-86801007
- 邮箱:1464856260@qq.com
- 网址:http://www.bubu8.com
- 地址:江苏省金湖县理士大道61号
利用数值仿真技术对涡轮流量计内部流场研究
发布时间:2020-11-26 08:00:31 点击次数:1881次
摘要:利用数值仿真技术对涡轮流量计内部流场进行了研究,目的是为优化涡轮流量计的结构设计提供指导。利用叶轮转速与平均力矩系数存在线性关系,提出两点法确定叶轮在力矩达到平衡状态下的转速。数值分析结果表明,前导流件叶片后形成的尾流影响叶轮入口的流体速度分布,继而影响叶轮的旋转稳定性;叶轮叶片压力面上靠近叶片前缘以及吸力面上靠近尾缘处存在压力突变区,易产生脱流现象;叶轮轮毂前后间隙区内流体受叶轮旋转影响而易产生漩涡流和明显的切向速度分量。
轮流量计是一种速度式流量计,利用叶轮的旋转速度来推导被测流体的流量大小,使得其内部流场分布对叶轮的旋转特性具有重要的影响。因此,利用数值模拟手段对涡轮流量计内部流场分布进行研究,从而为流量计的优化设计提供指导,无疑具有重要的意义。
过去,智能型液体涡轮流量计的研究主要集中在理论分析计算和实验研究等。基于作用在涡轮上的驱动力矩和各种摩擦力矩之间的力矩平衡方程,学者们建立了众多的涡轮流量计理论计算模型。其中,以Thompson和Grey提出的理论模型*具代表性。van der Kam等则利用实验研究了脉动流、漩涡流和速度剖面等因素对涡轮流量计特性的影响。近几年来,随着计算机技术和各种计算流体力学仿真软件技术的快速发展,数值模拟方法逐渐应用于涡轮流量计的研究中。
笔者基于流体力学计算软件Fluent建立涡轮流量计内部流场的数值计算模型,并利用模型对涡轮流量计前、后导流件结构对流场分布的影响,前导流件叶片后的尾流对叶轮进口速度的影响以及叶轮轮毂前、后端间隙内流场对叶轮旋转特性的影响等进行分析,其目的是为涡轮流量计的结构优化设计提供指导,减少流量计的压力损失,提高流量计的测量精度。
1、数值模拟
1.1基本模型
文中所研究的涡轮流量计的结构如图1所示。
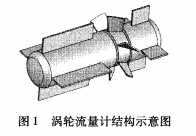
为了提高数值模拟精度,尽可能保留了涡轮流量计的结构特征,例如导流件轮毂与叶轮轮毂之间的间隙。流量计外壳内径为50mm,叶轮的主要参数如表1所示,流量计的设计流量为4~40m3/h。前导流件前端和后导流件的后端采用球形结构,前、后导流件叶片与叶轮叶片的间隙分别为12mm和7mm,导流件叶片厚度为1mm。导流件轮毂和叶轮轮毂同径,轮毂之间的间隙为2mm。
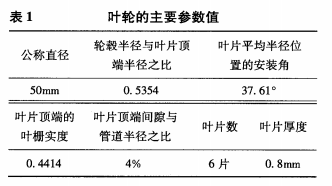
考虑到实际工程应用中涡轮流量计通常处于紊流状态下,故仅对这个流态下流量传感器内部流场进行了数值分析。笔者采用流体力学计算软件Fluent6.2作为数值模拟仿真工具,计算过程中所选用的相关模型及参数如下:
1)求解器选用分离式求解器;
2)紊流流动模型选用标准k-ε双方程模型,结合标准壁面函数进行数值计算,方程组中各项常数值给定为Fluent中的默认值;
3)空间方向上采用二阶迎风格式离散所有的控制方程,同时选用SIMPLE算法作为压力-速度耦合算法;
4)时间方向上采用二阶时间步进格式来进行时间离散。
1.2计算网格和边界条件
流体经过涡轮流量计时,冲击叶轮使叶轮旋转,流场经历了稳定、剧烈变化再到稳定的过程。为了保证进、出口处的流动都是稳定的,计算区域设定为:上游3D、下游10D,原点为叶轮的质心。考虑到叶轮部分的网格划分疏密对计算结果的准确性具有重要的影响作用,在网格划分时对叶轮表面的网格进行了适当的局部加密处理。前、后直管段采用六面体网格,前、后导流件部分区域采用六面体网格,其他区域采用四面体网格,叶轮部分全部采用四面体网格,计算区域内网格总数为96.64万个,其中叶轮部分的网格总数为45.02万个。
边界条件为:进口边界给定一均匀流速,出口边界给定出口静压,固体边界给定无滑移边界条件。
1.3运动区域模型的选择
在数值模拟中,涡轮流量计的叶轮处于旋转状态,而前、后导流件则处于静止状态。因此,计算区域可分为运动区域和静止区域。
关于运动区域中流动问题的建模,Fluent提供了多种可选模型,其中混合平面模型和滑动网格模型较适用于涡轮流量传感器内部流场的数值模拟。混合平面模型将各流域视为稳态,通过混合消除了流域通道之间由于周向变化而导致的不稳定(如尾流、激波和分流),从而得到稳态解。滑动网格模型则假定流动是不稳定的,用于转子和定子之间有强烈的相互作用和要求对系统进行精确的仿真的场合,但计算量比较大,对计算机内存的要求也比较高。笔者选用滑动网格模型来模拟叶轮区域的流场分布,主要是为了提高涡轮流量计内部流场的数值模拟精度,且能分析导流件叶片和叶轮叶片处于不同的相对位置时导流件后尾流对叶轮旋转特性的影响。
运动区域和静止区域的交界面则采用Fluent软件中提供的Interface边界条件。利用该边界条件,在界面处流场数据能有效地从一个区域向另一个区域传递。
1.4叶轮力矩平衡的判定方法
在涡轮流量计的内部流场处于稳定状态时,对任一入口流速,叶轮将以某一确定的角速度ω旋转,使作用在叶轮上的驱动力矩和阻力矩达到平衡。计算过程中,可以通过不断调整ω的数值,观察叶轮旋转是否达到力矩平衡,来确定叶轮的转速。然而这种计算过程非常耗时,在此笔者提出一种简便的确定方法。
数值计算过程中,可以通过利用Fluent软件提供的力矩系数Cm来监测作用在叶轮上的合力矩与参考力矩的大小之比,其计算公式为
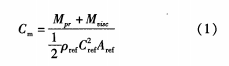
式中:Mpr和Mmin分别为压力矩和黏性阻力矩;Aref耐为叶轮叶片弦长与叶片高度的乘积;ρref耐为参考流体的质量密度;Cref为参考力矩系数。
图2即为叶轮在平衡转速下旋转时Cm的周期性变化过程。假定Cm为Cm值在一定计算时间内的平均值,计算时问通常约为一个叶轮轴的旋转周期。通过计算发现,Cm基本上与叶轮转速呈线性比例关系,见图3。Cm等于零所对应的ω则表示叶轮在此转速下旋转达到了力矩平衡。因此在实际计算中,可以选取两个转速进行计算,建立Cm与ω的线性关系,然后利用此关系确定叶轮的平衡转速。当然,预先能对叶轮处于平衡状态下的转速进行估计,缩小设定转速与平衡转速的范围,利用这种方法确定叶轮平衡转速的精确度将更加高。
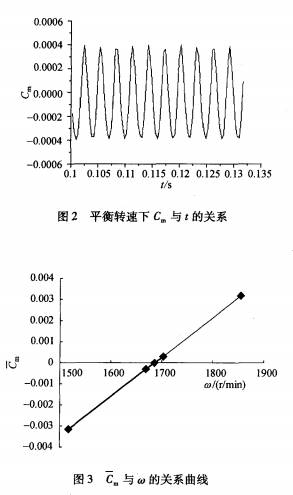
2、计算结果及分析
计算流体介质为水,其质量密度等于1.255kg/m3,运动黏度为1.46×10^-5m2/s,平均流速为3m/s。计算结果表明,叶轮的平衡转速为 1686r/min。
图4示出了涡轮流量计沿旋转轴方向上的速度演变过程。从图中可以看到,当流体进人前导流件,由于流道面积减少,流速增加。在前导流件后端,两相邻叶片之间流体速度分布已形成了环行通道中的速度剖面,固体壁面上存在边界层。受叶片尾流的作用,流出导流件的流体在叶片后缘附近存在明显的低速区。流体到达叶轮时,在自然耗散的作用下流速向均匀分布发展。紧靠叶轮叶片前缘,受叶轮旋转的影响存在一个流体速度加速区,这将导致随后的减速区内易发生流体分离现象。后导流件的流体速度演变则存在和前导流件相同的变化过程。
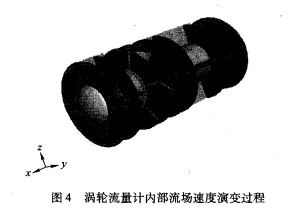
前导流件叶片后形成的尾流影响进人叶轮的速度分布,将导致叶轮叶片附近的流场分布很不均匀,*终影响叶轮的旋转特性。图5分别示出了在不同时间前导流件和叶轮之间间隙的不同横截面上轴向流速在半径r=0.02m周向上的分布情况。T=0时,前导流件叶片正对叶轮叶片,T=0.5T1时(T1为叶轮轴的旋转周期),前导流件叶片位于两叶轮叶片的中间位置。从图5中可以看到,尾流对速度剖面的影响主要体现在尾流区速度分布的变形上。T=0.5T1时,紧挨叶片后缘(x=-0.0175m)正对尾流区的轴向流速仅为0.25m/s,而*高流速则为 4.5m/s。靠近叶轮,尾流区的流速逐渐增加,在叶轮前(x=-0.O06m)*低流速升高到了3.75m/s。从图中同时可以看到,导流件叶片和叶轮叶片处于不同相对位置时,进入叶轮前流体速度分布情况并不一样,主要区别在于靠近叶轮的横截面上。T=0时,受叶轮叶片的影响,x=-0.006m横截面上的*低流速则为3.25m/s。叶轮入口速度的周期性变化也是造成合力矩系数Cm**间发生周期性变化的直接原因。可以预见,前导流件叶片与叶轮叶片的距离越远,叶轮的入口速度分布越均匀,Cm变化幅值越小,叶轮的旋转稳定性越好。因此在设计中,在确保导流件的整流效果合理的设计结构前提下,应适当减少导流件叶片厚度以及增加导流件和叶轮之间的间距,以降低尾流对叶轮入口速度分布的影响。
如图6所示,由于流体边界发生突变,在前、后导流件叶片后缘都有漩涡流的形成,增加了流量计的压力损失。因此设计导流件时,应考虑叶片的前后缘进行倒角处理。后导流件球形后端形成一个较大的回流区,同样也会增加流量计的压力损失。
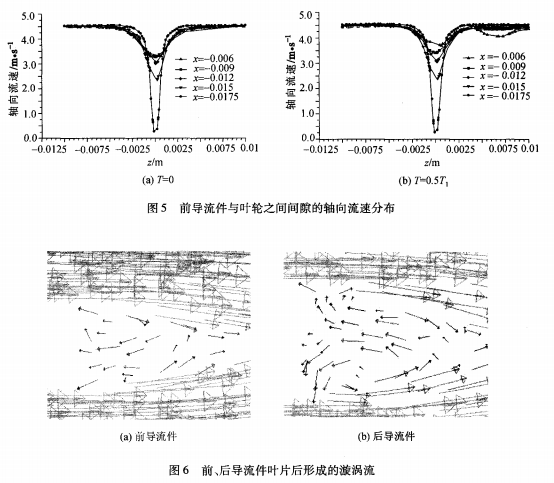
从图7的叶轮静压分布可以看到,在叶轮片的前缘形成了一个驻点,为高压区域。在接近叶轮轮毂表面以及叶顶处,由于存在边界层轴向流速减少,造成驻点压力减少,同时也会增加进入叶轮流体的攻角。由于叶顶间隙的作用,叶顶处的边界层对流体攻角的影响要比轮毂处的边界层对流体攻角的影响要小。在叶片压力面接近叶轮前缘处有明显低压区域,这种压力的快速过渡*易造成脱流现象,不仅增加了压力损失,也降低了叶轮旋转的稳定性。在叶轮叶片吸力面上接近尾缘处存在一个低压区,也易造成脱流现象。因此,应改善叶轮叶片前缘的流线型,使叶片前缘的高压区平缓过渡到叶片压力面接近前缘处的低压区,降低涡轮流量计的压力损失,增加叶轮旋转的稳定性。
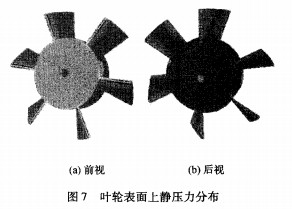
由图8可以看到,叶轮轮毂前、后端面与导流件之间缝隙中的流体受叶轮旋转的影响而具有明显的圆周运动。
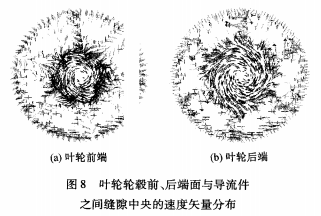
同时,叶轮前、后端缝隙中有明显的切向速度分量,而且靠近叶轮轮毂处有漩涡流形成,见图9。以上这些说明了叶轮与前、后导流件之间缝隙内流场分布对叶轮的旋转特性具有重要的影响。优化间隙内各轮毂端面的结构,使缝隙中的流体减少产生漩涡流以及切向速度分量,可降低传感器压力损失,同时可减少叶轮轮毂端面的黏性摩擦阻力。
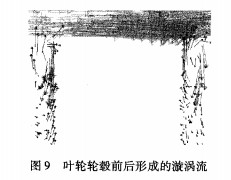
3、结论
本文利用所建立的数值计算模型对涡轮流量计内部的主要流场特征进行了分析,得到了以下结论:
1)前导流件叶片后的尾流影响进入叶轮入口流体速度分布,也是导致合力矩系数Cm**问发生变化的主要原因,从而影响叶轮的旋转特性。
2)叶轮叶片压力面上靠近叶片前缘有一个压力快速过渡区,*易造成脱流现象,增加了流量计的压力损失,也降低了叶轮的旋转稳定性;叶轮叶片吸力面上靠近叶片尾缘有一个低压区,也易造成脱流现象。
3)叶轮轮毂前、后间隙内的流场受叶轮旋转的影响而易产生漩涡流以及明显的切向速度分量。
在未来工作中,仍需对涡轮流量计内的其它流动现象进行分析,以提高流量计的测量精度。本文已对前导流件叶片后的尾流对叶轮进口速度的影响进行了分析,今后将进一步研究间隙距离不同的情况下尾流对叶轮旋转特性的影响。
相关资讯
- 气体涡轮流量计安装直管段要求
- 气体涡轮流量计的结构与工作原理
- 气体涡轮流量计的产品特点和适用范围
- 气体涡轮流量计选型指南与外形尺寸
- 涡轮流量计的常见故障及排除
- 涡轮流量表怎么调节
- 涡轮流量计安装直管段要求
- 涡轮流量计的适用场合与量程范围
- 涡轮流量计由什么组成
- 涡轮流量计的工作原理
- 压力对涡轮流量计精度的影响
- 液体涡轮流量计使用常见问题
- 液体涡轮流量计的使用场合
- 液体涡轮流量计怎么接电
- 涡轮流量计的使用范围
- 涡轮流量计安装条件与环境要求
- 涡轮流量计安装在什么位置
- 液体涡轮流量计设置方法
- 气体涡轮流量计使用环境
- 气体涡轮流量计使用注意事项
- 气体涡轮流量计怎么清洗
- 气体涡轮流量计适用范围
- 气体涡轮流量计为什么要加油
- 气体涡轮流量计波动大解决办法
- 气体涡轮流量计安装距离要求
- 气体涡轮流量计安装注意事项
- 气体涡轮流量计应用范围
- 气体涡轮流量计常见故障有哪些
- 提高气体涡轮流量计精度的方法
- 气体涡轮流量计精度等级