产品目录
液体涡轮流量计
液体流量计
水流量计
油流量计
气体涡轮流量计
椭圆齿轮流量计
电磁流量计
涡街流量计
蒸汽流量计
孔板流量计
旋进旋涡流量计
热式气体质量流量计
转子流量计
浮子流量计
靶式流量计
气体流量计
超声波流量计
磁翻板液位计
浮子液位计
浮球液位计
玻璃管液位计
雷达液位计
超声波液位计
投入式液位计
压力变送器
差压变送器
液位变送器
温度变送器
热电偶
热电阻
双金属温度计
推荐产品
联系我们
- 金湖凯铭仪表有限公司
- 联系电话:15195518515
- 在线客服:1464856260
- 电话:0517-86801009
- 传真号码:0517-86801007
- 邮箱:1464856260@qq.com
- 网址:http://www.bubu8.com
- 地址:江苏省金湖县理士大道61号
关于气体涡轮流量计结构与压损间的关系
发布时间:2021-03-10 06:44:58 点击次数:3153次
摘要:对DN100气体涡轮流量计的关键部件之一前导流器引起的流量计压力损失进行试验测量和数值计算。对比分析两种不同结构前导流器对压力损失的影响,发现前导流器的结构变化不仅影响该部位的气流速度分布,使当地压力损失发生变化,更重要的是对后面各部件内的气体流动速度梯度和压力恢复也有明显影响,使总压损失进一步放大或减小。数值计算通过分析流动参数的变化从流动机理上解释了结构与压损间的关系。
涡轮流量计是一种速度式叶轮流量测量仪表,它利用置于流体中的叶轮的旋转角速度与流体流速的正比关系,通过测量叶轮转速得到流体流速,进而得到管道内的流量值。涡轮流量计以其结构简单、精度高、流通能力大而被大量应用于能源动力、水利输运和天然气计量等工业领域中。在选用涡轮流量计时,除要求其准确度高、量程宽和起始流量小外,压力损失也是关键指标。具有较小压力损失的涡轮流量计可减少输运流体的能量消耗,进而节约能源,降低输送成本。国外较早就开展了对涡轮流量计的数值计算研究,随着所采用计算方法和模型精度的提高,在改善涡轮流量计性能方面取得了显著进步。我国多年来则侧重于提高电信号转换精度方面的研究,且偏重于试验,对流量计流动性能与结构相互影响的理论与数值研究很少。本文拟通过对传统和流线形前导流器结构对涡轮流量计性能影响的数值模拟计算,并与试验测量的比较,确定数值模拟方法的有效性,同时分析前导流器结构对性能的影响机理。
1、试验模型与测量装置
1.1流量计结构与改进
涡轮流量计结构示意图如图1所示,主要组件包括前导流器、叶轮、支架以及后管段。流体从机壳进口流入,*先经过前导流器,前导流器对流体流动有如下两个重要作用:
① 收敛作用。气流在此处由管道流转换为环形通道流,速度增加而压力减小,避免流动分离产生大的涡旋运动。
② 导向作用。导流叶片可避免流体自旋而改变对叶轮叶片的作用角度,保证计量的准确度。
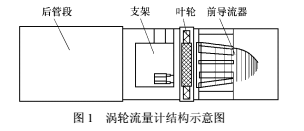
体通过流量计的压力损失与介质的密度、流速等有关,其计算公式为
?p=α·ρ·v²/2 (1)
式中,?p为压力损失,α为压损系数,ρ为介质密度,v为流速。
由于ρ和v为流体流动参数,不能随意增减,因此只能尽量减小压损系数α,以达到降低压损的目的。压损系数除了受流体粘性、管径及管长等因素影响外,与流量计内部各部件的几何结构有密切关系。文献通过试验发现叶轮的形线、叶片数对压力损失的影响较小(≤3%),因前导流器对流量计有着重要作用,故将传统的球形前导流器改进为流线形,考察两者在流动减阻方面的不同,进而分析对流量计性能的影响程度。DN100涡轮流量计改进前后的前导流器结构如图2所示,几何参数见下表。
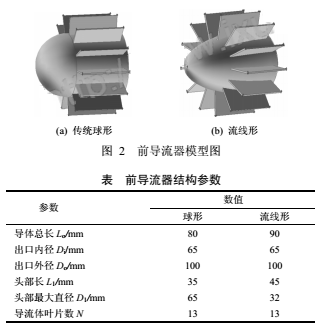
1.2试验装置
气体涡轮流量计的流量与压力测量装置如图3所示。主要包括四部分:测量段部分、稳压罐、标准表、引风机部分。测量段部分包括前直管段、“U”形管或斜管微压计、气体涡轮流量计、后直管段以及检测台;引风机部分包括流量调节阀、引风机以及消声器。
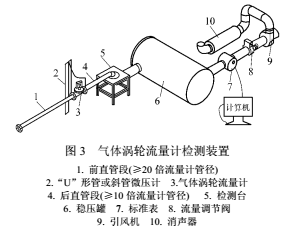
被测流量计安装在测量段中,前直管段长度大于20倍被测气体流量计管径,后直管段长度大于10倍流量计管径,“U”形管或斜管微压计连接在被测流量计的入口和出口处,用于测量流量计的压力损失。标准表为罗茨气体表,精度0.5级,用于计量流经被测流量计的气体流量。标准表与计算机连接,由计算机进行实时监控,输出瞬时流量,并显示累计流量值。引风机用于产生管道气体流量,通过阀门调节流量大小,引风机出口端安装有消声器以降低噪声。
2、压力损失数值计算
通过数值方法模拟两种前导流器结构下流量计的内部流动,将模拟结果与试验宏观测量参数进行符合度对比,进而再对速度、压力等微观流动参数进行详细分析,得出影响压力损失大小的流动规律。
2.1模型建立与网格划分
在数值求解前,*先建立流场的计算几何模型。数值计算对象与试验流量计相同,均为DN100气体涡轮流量计。按照流量计的结构特点,采用分块建模方法,将计算流场分割为前导流、叶轮、支架及后管段(尾流)四个部分,如图1所示。
在网格生成过程中,对前导流器和叶轮旋转区域采用非结构化网格,网格数为300 000;叶片及导流体壁面处建立5层边界层网格,*小尺度为0.1mm;支架和尾流部分分区生成结构化网格,以节省计算时间,网格数为200 000;对前导流器和叶轮叶片根部附近流动变化剧烈的区域进行网格加密处理,以提高网格质量,得到较详细的流动信息。两种前导流器配以相同的叶轮(叶片数20)和支架。生成后的计算网格总数均为550 000左右。
2.2数值计算方法
数值计算时,必须建立正确的流动物理模型。连续性方程、N-S运动方程是描述流体流动的基本控制方程组。本文采用将雷诺平均N-S方程组与几种湍流模型相结合的数值求解方法进行了求解对比,应用雷诺应力模型解的收敛性不好,而Spalart-Allmaras模型精度不够,*终确定采用k–ε两方程湍流模型解决内流方程组的封闭性问题,并达到求解目的。
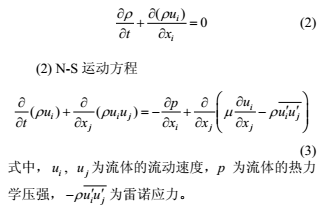
从上述流动方程出发,针对流量计的具体流动特点进行了如下简化:将叶轮旋转部分设定为相对旋转坐标系后,流动为定常,即不考虑方程中的时间项;考虑到绝大部分流动速度小于50m/s,忽略速度变化对密度的影响,即假定流动为不可压。
方程的求解方法采用SIMPLE算法。以“有限体积法”作为流场的数值离散方法,方程离散过程中采用二阶精度的迎风差分格式。
由于流场结构复杂,对湍流雷诺应力的模拟采用普适性*好的标准k–ε模型
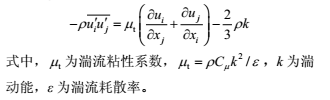
湍动能k和湍流耗散率ε则通过对其赋初值后由相应的k方程和ε方程求得。
计算中应用的边界条件如下。
入口:给定相应流量下的主流速度值。
出口:满足质量守恒,min=mout。
固壁:壁面函数法。
叶轮部分采用旋转坐标系,给定相应流量下的叶轮转速。
3、计算与试验结果分析
3.1压力损失值的比较
图4为两种前导流结构下总压损失与流量的关系曲线。图4b为图4a在量程为0~400m³/h区间的曲线图。
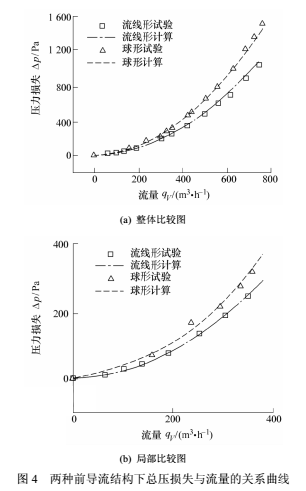
由图4可知,两种结构下的计算与试验值符合很好,误差在全量程范围内均小于5%。在小流量(≤200 m³/h)区,无论是计算值还是试验值,两种结构的压损值相差非常小,说明前导流结构在流量较小时对压损的影响不明显。随着流量的增大,结构导致的压力损失出现了较大差别,明显看到,流线形与球形的数值差距越来越大,在*大流量处(约 750 m³/h),球形压损比流线形增大约30%。
试验和计算结果均显示,气体流经涡轮流量计的总压损失随流量基本呈二次方增长趋势,即?p=αQ²,这与式(1)是一致的。不同结构的前导流,二次函数的系数α不同。对于流线形前导流,该系数显然较小。按照式(1)的分析,压损系数a代表流动过程中各种因素引起能量损失的综合能力。由此可以推断,流线形结构更符合流动的要求,使流动过程中的能量损失被削弱,从而提高了流动性能。流量越大,这种改善越明显。
计算过程中还发现,在*小流量下(≤30 m³/h),计算与试验的相对误差明显增大。例如在流量为30 m³/h 时,压力损失测量值为5Pa,而计算值为2.6Pa,误差达48%。分析原因是由斜管微压计的测量精度引起,其读数误差为0.5mm,当斜管倾斜30°时,产生的相应水柱误差约为3Pa,当实际压差很小时容易引起较大的读数误差,鉴于此,本文计算与试验的比较范围大于50 m³/h。
3.2数值模拟结果流场分析
为进一步定量考查前导流器结构对流场特别是对压力的影响,将两种结构下数值模拟流场的压力与速度分布规律进行了对比分析,从流动机理角度对结构与压力的关系给予考查。
图5为两种前导流器结构水平中心断面上的压力等值线分布,宏观上,图5a、5b的压力变化趋势是一致的:在前导流器、叶轮和支架部分,压力均不同程度地降低,由支架进入尾流区后,压力逐步上升。
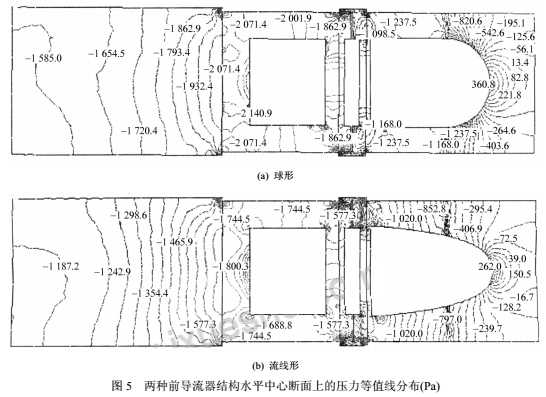
仔细观察,两者在量值上存在较大不同:
①在前导流器部分,球形的前半部压力变化剧烈,后半部几乎不变化,流线形的压力变化体现于整个流道中,较缓和,结果使球形(1237.5 Pa)进、出口的压差(入口相对压力0Pa)明显高于流线形(1 020.0 Pa),可见流道逐渐收缩有利于减小压力损失。
②叶轮部分的压降,球形约为630Pa,流线形为560Pa。在该流域,部分压能转换为动能驱动叶轮旋转,流线形压力损失略低于球形。
③在支架环形通道中的压力损失,球形为208.5Pa(支架前端压力2071.4Pa与末端压力1 862.9 Pa之差),流线形为167.2Pa(支架前端压力1 744.5Pa与末端压力1 577.3Pa之差),也是流线形低于球形。
④由支架出口进入突然扩张的尾流部分后,气流减速增压,在此过程中球形压力由–2 071.4Pa上升为–1 585.0Pa,增值486.4Pa,流线型由–1 744.5Pa上升为–1 187.2Pa,增值557.3Pa,流线形的压力回升速度快于球形。
上述四部分压力变化的叠加体现为涡轮流量计的总压损,球形为1 585Pa,流线形1 187Pa,球形比流线形高33%左右。
图6为与图5相同位置上的速度等值线分布。在前导流器处,可看出对应压力变化剧烈的区域,速度变化也较大。球形头部速度急剧增大、直管段速度几乎不变的分布趋势使其中心出口速度(47.0m/s)较大(流线形45.2m/s),在同流量下表明球形前导流器具有较大速度梯度。当气流进入尾流部分后,由于流道突扩,在支架的背面形成明显的低速涡区,之后管壁附近速度降低,中心区主流速度回升,速度值被逐渐拉平,对应压力也逐步回升。可看到,至出口断面,流线形的速度不均匀*大差值为6.0m/s,球形为9.4m/s,即球形的出口速度梯度更大,压力回升则相应较慢。
综合图5、6,速度的分布和变化与压力损失的大小密切相关,流线形前导流器不仅使当地的气流速度分布较球形更均匀(梯度较小),还影响其后的流场速度变化程度,从而使各部分的压力损失连锁减小,达到明显降低总压损的目的。
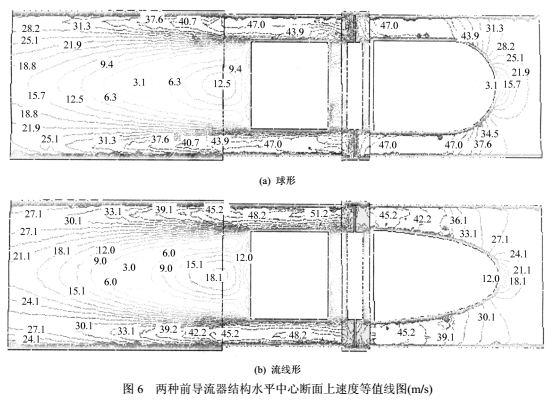
4、结论
对传统球形和改进的流线形两种前导流器结构下涡轮流量计的试验测量和数值计算结果表明,在小流量(≤200 m³/h)下,两者压损几乎相同,即结构对压力损失的影响很小;随着流量增大,压损差值越来越明显,在*大工作流量(750 m³/h)下,球形压损比流线形增加了约33%。改进后的流线形前导流器通过改善气流在当地及随后各部件中的速度和压力分布,使速度梯度降低,压力恢复加快,从而达到明显降低总压损的目的。
计算与试验的对比结果显示,采用数值计算方法可以有效地模拟涡轮流量计内部的气体流动从而给出正确的压力损失值,是进一步深入研究涡轮流量计的可靠工具。
相关资讯
- 气体涡轮流量计安装直管段要求
- 气体涡轮流量计的结构与工作原理
- 气体涡轮流量计的产品特点和适用范围
- 气体涡轮流量计选型指南与外形尺寸
- 气体涡轮流量计使用环境
- 气体涡轮流量计使用注意事项
- 气体涡轮流量计怎么清洗
- 气体涡轮流量计适用范围
- 气体涡轮流量计为什么要加油
- 气体涡轮流量计波动大解决办法
- 气体涡轮流量计安装距离要求
- 气体涡轮流量计安装注意事项
- 气体涡轮流量计应用范围
- 气体涡轮流量计常见故障有哪些
- 提高气体涡轮流量计精度的方法
- 气体涡轮流量计精度等级
- 气体涡轮流量计的技术参数
- 气体涡轮流量计不准原因
- 气体涡轮流量计的优缺点
- 气体涡轮流量计的用途
- 气体涡轮流量计接线图
- 气体涡轮流量计种类
- 用气体涡轮流量计测量天然气流量
- 气体涡轮流量计的优点
- 气体涡轮流量计使用方法
- 气体涡轮流量计的选型表
- 气体涡轮流量计结构图
- 影响气体涡轮流量计测量精度的因素及措施
- 气体涡轮流量计维护保养
- 气体涡轮流量计特点